Learn About Popular Garage Floor Coating Options
There are many different styles of garage floor coatings available on the market today. We won’t go into too much detail in this article, but here are the basics.
Flake Floors
This is the most common type of garage floor coating, especially those done by professionals. The two common options are “random flake” and “full-flake”. Random flake floors have a light-medium, random spread of decorative color flake broadcast into the wet material. It looks like speckles in the floor, and it adds color, and contrast to take the eyes off of imperfections in the floor.
On a full-flake coating, the wet basecoat is completely saturated with flake, until it can’t hold any more. This creates a much thicker coating. Picture a glass of water that is half-full. Now add ice to the glass until it is full, and the fluid level is at the top. That is the effect you get from this full-saturation of flake.
In general, flake floors offer the best value for residential garages, especially the full-flake systems.
Other Floor Coating Options
There are a few other popular options for garage floor coatings. “Neat” floors are made up of one or more coats of materials, without any sort of aggregate in them. Neat floors really need several coats of material, or special materials, to perform well. Even then, they are more likely to show wear and tear. For this reason, a flake floor usually offers a better value.
Shop floors and Quartz floors use a silica or quartz aggregate in lieu of flake. These aggregates increase the thickness and compressive strength of the floor. Shop floors use silica, a manufactured sand, and are usually topped with a solid-colored topcoat. Quartz is like a decorative sand. On these floors, the Quartz itself actually gives the floor it’s color, and it is topped with protective clearcoat.
Metallic epoxy floors consist of a fine metallic pigment suspended in a clear resin. It creates a random, marbled-effect. The material can be agitated while wet to create different visual effects. They can be done using a single color, but more often multiple colors are used to create amazing finishes. These floors require more preparation work, and more material than other systems. For these reasons, plan on paying more for this type of coating. Another consideration with metallic floors, is the installer. Metallics are a form of art, so you want to see lots of examples of the installers work. Choose an installer whose style you like. This isn’t one you want done by a labor crew.
Start By Looking At The Company Itself
Find Out If They Are Licensed And Insured
Are They Licensed? Many states require some form of contractor’s license to do floor coatings. If your state does require a license, you can ask the contractor if they are properly licensed, but it’s best to look it up yourself. You can normally lookup contractor’s licenses through the state website.
Your state may also require that the contractor be bonded. Ask the contractor for the bond number and certification. If you have legitimate issues with the work, you can contact the surety company directly.
Are They Insured? At minimum, the contractor should carry robust General Liability insurance. This policy protects you in the event of any damage to your property.
Research The Contractor’s Reputation Online
You can find out anything you need to know on the internet. You can start by checking their reviews on Google, Facebook, and Yelp.
Look At Their Bad Reviews
Don’t just look at their aggregate star rating. If they have any bad reviews, read them and see if there is a pattern. Even the best contractor is going to have issues here and there. Focus on how they deal with issues when they have them. If there is a pattern of the same issue, or an unwillingness to resolve issues, that is a huge warning sign.
Look At Their Positive Reviews
Any business can go on websites like Fiverr.com and buy as many 5-star reviews as they want. Genuine reviews typically include keywords related to the product, description of the work, and other useful information such as the city. Generic reviews such as “Great Work”, especially if there are a lot of them, are another warning sign.
Better Business Bureau
The BBB is trusted resource for finding good contractors. Unfortunately, their grading system doesn’t always paint an accurate picture. Don’t just look at their score, or their reviews. LOOK TO SEE IF CUSTOMERS HAVE FILED ANY DISPUTES! If more than one dispute has been filed, see if there is a pattern, and if the contractor made an honest effort to resolve each issue. Again, this is a huge warning sign.
Ask For References?
You can ask your contractor for references, but don’t expect much. Even the worst contractor can come up with a couple of references. Online reviews and rating sites like Angieslist.com provide more honest information.
Don’t ask to see other customer’s floors either. This is bad policy, and you don’t want a contractor bringing strangers into your home. It is our policy to respect our customer’s privacy, and safety. With all of the resources available to you online, this is not necessary anyway.
How Long Have They Been In Business?
This is important, but equally important is how long they have been in the industry. I had personally installed more than 1000 garage floor coatings before I started my own business. That being said, someone might be an excellent practitioner but a lousy businessman. You really want to get an understanding of their industry experience, and balance that with their business history.
Get Estimates, Contracts, and Warranties In Writing
You don’t want to call around and get pricing over the phone. You want your estimates in writing. At minimum, each estimate you receive should answer the following questions:
1. What method of surface preparation will be performed?
2. What type of coating is the estimate for (i.e. full-flake)?
3. How many coats of material will be used?
4. What is the overall thickness, or thickness of each individual coat?
5. What is the warranty?
If you can’t answer these questions using the information in the estimate, this is another big warning sign. You wouldn’t get an estimate to have your kitchen floor tiled, that didn’t specify the exact type of tile, and other details, right?
Moisture Testing
There is a lot of bad information about moisture issues and coatings out there. Let’s simplify the subject for easy understanding. First, let’s clarify something. We are referring to moisture that is passing through the concrete. The source of this moisture is usually the soil beneath the slab. We are NOT talking about moisture on the surface of the floor.
Performing proper moisture tests on a garage floor is not very realistic and can be cost prohibitive. For starters, most methods require that the room, and the slab, are acclimatized prior to testing. In most cases, garages are not climate controlled, so this is not feasible. The most accurate test involves coring holes in the slab, installing expensive digital sensors, and then taking readings for several days. This type of test can cost as much or more than a typical garage floor coating.
Finally, even if proper moisture tests are performed, conditions can change later. Installing a coating alone can change the moisture conditions, because it effectively seals the concrete preventing moisture from escaping from the surface.
If there are signs of moisture problems in the concrete, you might want to perform additional tests or inspections before moving forward with the coating. Common signs of moisture issues include dark or damp looking areas of concrete and efflorescence.
Here are a few pictures of garage floors with warning signs of moisture issues.
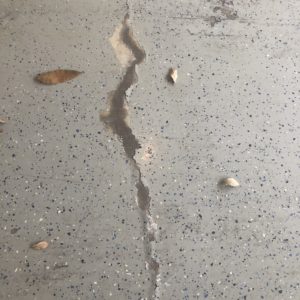
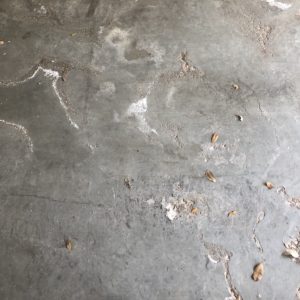
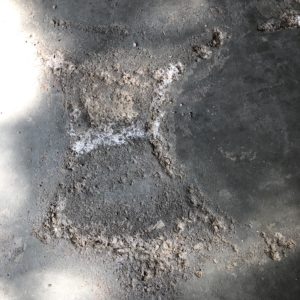
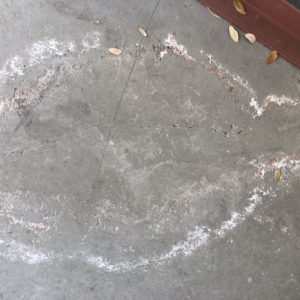
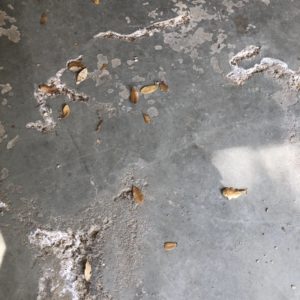
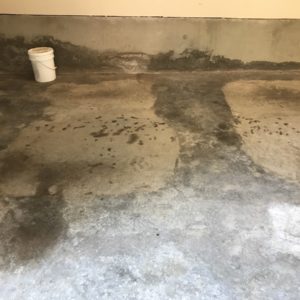
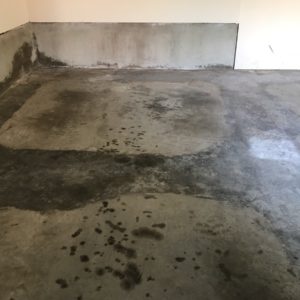

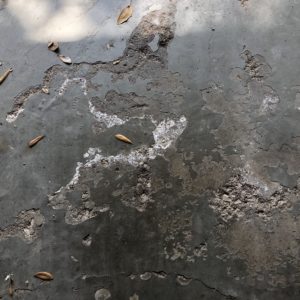
Method Of Surface Preparation
There are only two types of surface preparation that professional coatings companies use – diamond-grinding and shot-blasting. Residential garage floor companies primarily diamond-grind, and this method is quickly becoming the most prominent method in the commercial world.
A large, planetary diamond grinder should be used. Smaller machines such as diamond cups, and diamond brushes are inferior, and may not produce the necessary textured-profile, called a Concrete Surface Profile (CSP).
Dust Extraction Equipment must be run when diamond-grinding or shot-blasting. These machines are industrial vacuums with HEPA filters that attach directly to the machines. There should be very little airborne dust during surface preparation.
Acid-etching, pressure washing, sanding, and other methods are not used by professional coating contractors, and are not approved by most manufacturers, or the International Concrete Repair Institute.
Repairs
At minimum, basic repairs need to be performed before applying a coating. Specifically, cracks should be repaired and sealed. On higher-end coatings, lots of repairs and detail work should be performed to get the concrete looking good and ready to receive the coating.
Repairs should be performed using polymer-based materials. These materials form strong bonds with the concrete, and when used properly they can permanently repair cracks and damage.
Understanding The Coating Materials
You may already be aware that epoxy is not the only material being used these days. If you’ve started shopping around, you may have heard the terms “polyaspartic” and “polyurea”. You’ve also probably read things like “Our material is 10x stronger than epoxy!” or “Our proprietary technology is 100x better than epoxy!” So, what does all of this puffery mean? Let’s break down the common materials into a few simple groups and understand how to choose the right stuff.
Epoxy
Epoxy is the traditional material used in garage floor coatings. The term “epoxy” is also used generically to describe resinous floor coatings in general. Epoxy is still the most commonly used material used today, and it is also used in combination with other materials.
Epoxy is not inherently UV-tolerant, and is known to “Amber”, or turn yellow over time; especially when exposed to sunlight and certain types of commercial lighting. Certain types of epoxies are more prone to staining, and discoloration from heat (such as hot tires). For these reasons, it is not always the best choice for a topcoat.
However, good epoxy offers excellent adhesion with the concrete. It can be applied in thick coats providing a high-build. And, it is usually much less expensive than materials like polyaspartic and polyurea. For these reasons, it is an excellent choice for primer, basecoats, and build coats.
Polyaspartic/ Polyurea
Polyaspartic and Polyurea are possibly the most common topcoats in use by professionals today. Polyaspartic is actually a member of the polyurea family. These materials are inherently tolerant to UV, and very resistant to abrasion, chemicals, and staining. For these reasons, these materials are an excellent choice for a topcoat.
In the residential garage floor world, there is trend of using polyaspartic for every stage of the coating – primer, build-coat, and topcoat. The reason for this is that it cures incredibly quickly. Subsequent coats can be applied in as little as 45-90 minutes. This allows for a 1-day installation process. This might be beneficial to the homeowner under certain circumstances. It’s definitely beneficial to us as contractors – one trip to the job, multiple jobs per day, etc.
But it’s not necessarily the best product or the you, the homeowner. These coatings tend to have a lower overall thickness. Also, it cures so quickly that the reaction is occurring rapidly as it’s being applied to the floor. When applying the first coat direct to concrete, you want a material with ample working time. You want the material to thoroughly wet the concrete before it starts to gel. This way it forms a strong, permanent bond with the concrete. Polyaspartic cures so quickly, that there is an increased risk of the material “gelling” before it has time to bond with the concrete. We have seen cases in the Dallas/Ft. Worth area where a professionally installed polyaspartic coating has failed, and the contractor who installed it refused to honor the warranty.
So, just because polyaspartic can technically be used for every stage, doesn’t make it a good idea. Using epoxy for a basecoat allows for a more reliable bond with the concrete, and a higher-build basecoat. Then you can put polyaspartic/polyurea up on top as a clearcoat, for its uv-tolerance, and resistance to abrasion and staining.
What Brand Of Materials Will Be Used?
True professionals do not buy materials at home improvement stores, or paint-supply stores. Typically, they will purchase their materials direct from the manufacturer, or from a bigger distributor. This allows them to get better pricing on higher-quality materials.
Contractors should sound proud of the materials they use, and they will may use them as a selling point but understand that it may be puffery. Statements like “Our material is 10x stronger than epoxy!” are examples of puffery.
Upon request, they should be willing to provide the manufacturer’s information, along with the Technical Data and SDS on each material they will use. If they are unwilling, this a big warning sign.
What Is The Warranty?
Most professional garage floor coating companies are offering lifetime warranties these days. Usually the warranty covers delamination & peeling, certain types of stains, and may include discoloration and color-shifting. This is not a finish warranty, and it does not cover damage from outside forces, or changes in the substrate. In most cases, these warranties apply only to the current homeowner, and do not transfer in a sale.
Time To Choose Your Garage Floor Company
There are many things to consider when choosing a contractor to install your epoxy garage floor coating. Hopefully this article helps your decision-making process easier. Take time to look at their reputation online, beyond their star-rating. Read the bad reviews, and look to see if the good reviews seem genuine. Check for disputes filed with the BBB, and even check RipoffReport.com.
Diamond-grinding and shot-blasting are the only methods of surface preparation that should be used. At minimum, cracks should be repaired, but ask about how much repair and detail work will be done. Repairs should be done using a polymer material, not cementitious patch products.
If there are signs of moisture issues, or other areas of the home have had moisture related issues, you may want to address that further before installing the coating. Generally speaking, have professional testing done is difficult and expensive when it comes to garage floors. You’ll have to use your best judgement on this issue.
Don’t get caught up in all the hype about who’s materials are better or stronger. The fact is epoxy is still the most common material used in floor coatings. It just needs to be a good, 100% solids epoxy. Then you want polyaspartic or polyurea for the topcoat. Remember, if the contractor advertises two or more topcoats, this is a sign that they are using a highly-diluted product. A good material can achieve the desired thickness in a single coat.
The warranty should cover delamination failures such as hot-tire peel, and most warranties these days are at least 10-years, if not a lifetime guarantee.
Finally, trust your instincts! If you have a bad feeling about a particular contractor, either do more research on them, or just dismiss that estimate. Like any business transaction, you should feel comfortable with the person you are doing business with. Your relationship with your contractor should be built on mutual trust. Remember, a good contractor is looking for customers that offer value, just as much as you’re looking for a good value on your garage floor coating!